Why is performance testing of liners important in tailings containment?
- benlewis24
- May 14, 2024
- 3 min read
In the mining industry, the importance of safely containing tailings—byproducts of mineral processing—is paramount. Tailings Storage Facilities (TSFs) are critical infrastructure designed to isolate these often toxic sludges from the environment. When used in these facilities, liner systems and their performance are key factors in ensuring long-term safety and compliance with environmental standards. But why is rigorous performance testing of these liners so crucial? Let’s explore.
Critical Exposure to Risk Factors Liners in TSFs are often exposed to a complex mixture of chemicals and heavy metals. These substances can degrade liner materials over time, compromising their integrity. Additionally, environmental factors such as UV radiation and extreme weather conditions can further accelerate this deterioration. Without robust performance testing, the long-term durability of liners remains uncertain, posing significant risks.
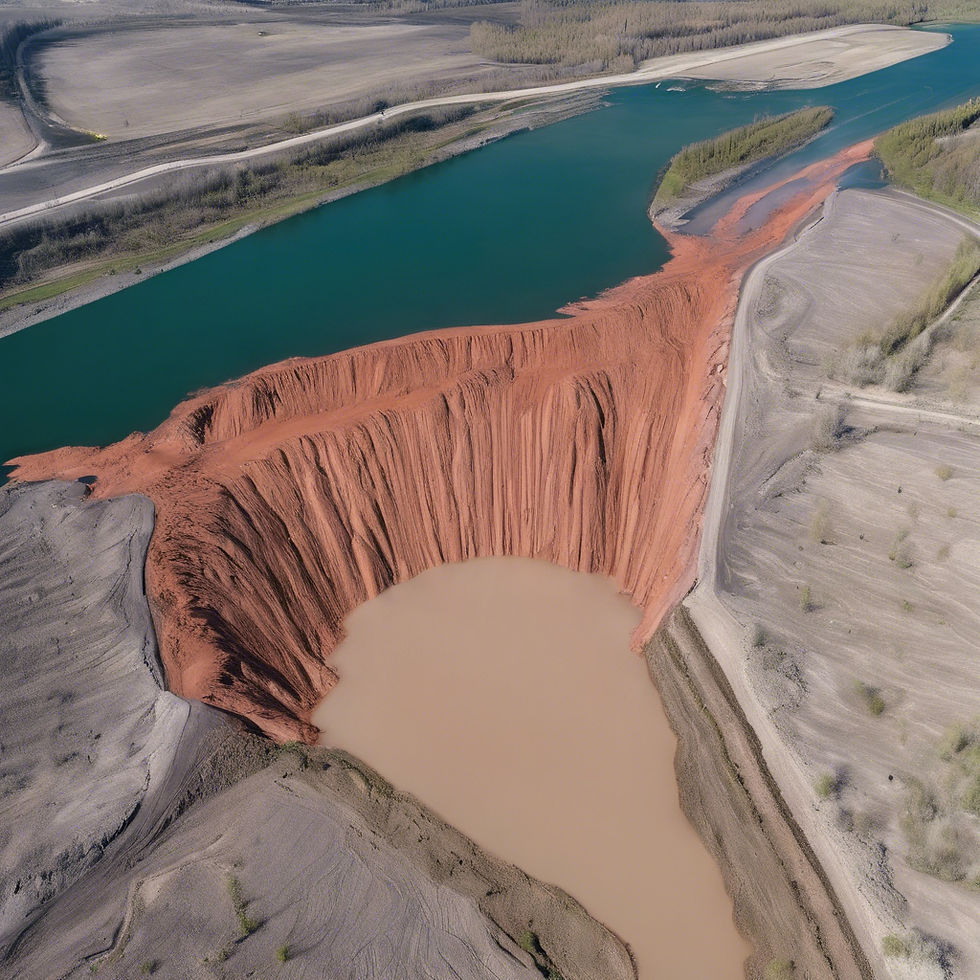
Diverse Performance of Geomembranes Under Real-World Conditions
Despite having identical technical data sheets, not all geomembranes perform equally under the same field conditions. Common materials like High-Density Polyethylene (HDPE) are typically evaluated under laboratory conditions that may not accurately represent the challenges encountered on site. Standard tests such as High-Pressure Oxidative Induction Time (HPOIT) and Oxidative Induction Time (OIT) measure performance under controlled heat and UV exposure. However, these tests rarely account for the complex chemical environments that can significantly alter the performance and durability of the liners.
For high-risk assets, it is crucial to conduct site-specific testing that considers the unique chemical make-up of the tailings. Such testing can significantly differentiate performance outcomes, leading to a more accurate estimation of a liner's lifespan and overall value. The same principle applies to Bituminous Geomembranes (BGMs), Geosynthetic Clay Liners (GCL), and other polymeric liners that vary in composition and additives according to the manufacturer's formula. By acknowledging and testing for these variations, stakeholders can ensure a liner system that meets and exceeds expectations, providing extended reliability and better return on investment. This proactive approach is essential for maintaining the integrity of tailings containment systems and protecting the environment from potential hazards.
The Consequences of Failure The stakes in tailings containment are extraordinarily high. Failure of a liner system can lead to disastrous environmental contamination and severe public health crises. Heavy metals and toxic chemicals can leach into groundwater and surface water, affecting drinking water supplies and harming aquatic life. The social, environmental, and economic repercussions of such incidents can be catastrophic, highlighting the necessity for exhaustive testing and reliable liner performance.
Regulatory Expectations and Life Span of Liners Globally, regulators have stringent expectations for the life span of tailings containment assets. These expectations can extend to centuries, underscoring the need for liners that can perform reliably over long periods. Regulators typically set clear guidelines on acceptable leak rates to mitigate environmental impacts. However, the actual enforcement and monitoring of these guidelines can vary, emphasising the importance of proactive and rigorous performance testing by the facility operators themselves.

Design Challenges and Risks In some large tailings facilities, the lack of adequate drainage systems beneath liners is a critical design flaw. This can lead to water pooling below the liner system and increased pressure on the liner, exacerbating the risk of rupture and leakage. Combined with unclear or minimal guidelines on allowable leak rates, such design oversights can lead to underwhelming and potentially hazardous containment solutions. It is vital that designs not only comply with regulatory standards but also incorporate robust safety margins to manage unexpected stresses on the liner systems which are rapidly becoming standard practice in tailings, irrespective of their chemical nature.
Conclusion Performance testing of liners in tailings containment is not just a regulatory compliance issue; it is a fundamental aspect of responsible mining practice. With the potential environmental and public health hazards at stake, ensuring the integrity and efficacy of these containment systems through rigorous testing is a critical duty for all stakeholders involved. As the demands on these systems increase and regulatory frameworks evolve, the industry must prioritize advancements in liner technology and testing methodologies to safeguard both the environment and public health against the risks of tailings contamination.
Call to Action The mining industry, regulators, and environmental scientists must collaborate closely to enhance liner testing protocols and design standards. By doing so, we can ensure that tailings containment systems are not only designed to meet today’s standards but are robust enough to handle the challenges of tomorrow.
Comments